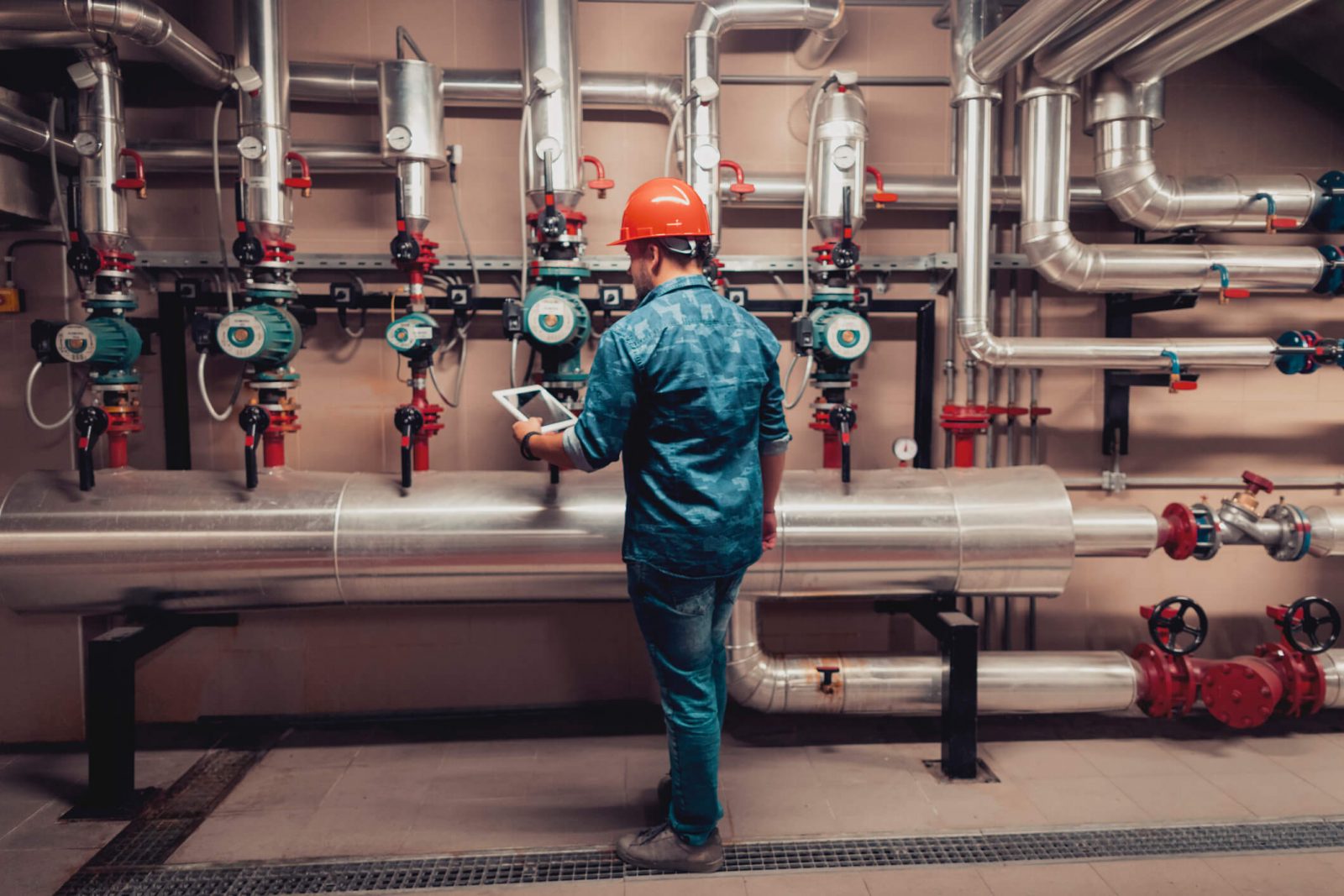
Se você trabalha com manutenção já deve saber como é importante a boa gestão dessa área. Para que o gerenciamento do setor de reparo e prevenção de defeitos de equipamentos seja feito de maneira eficiente, é preciso utilizar algumas ferramentas. Uma delas é a análise de falhas.
Ela é responsável por diminuir, consideravelmente, o número de máquinas paradas. Essa é uma técnica aplicável à gestão de manutenção de qualquer empresa e envolve processos práticos e simples.
Inicialmente, a aplicação pode precisar de ajustes e aprimoramento, porém, uma vez consolidada a sua implantação, os benefícios são diversos. Quer saber o que é exatamente a análise de falhas, sua importância e aplicação prática? Continue lendo este post!
Afinal, o que é análise de falhas?
É uma estratégia usada pelas equipes de gestão em manutenção que visa a minimizar, ao máximo, a quantidade de imperfeições de um equipamento, processo ou produto. Essa técnica busca monitorar defeitos antigos, investigá-los e propor ações corretivas e preventivas.
Existem diversos recursos usados para fazer com que o método funcione, mas é preciso contar com o engajamento da equipe e a consistência da aplicação ao longo do tempo. Os resultados não vão aparecer logo que a empresa começar a aplicar a análise de falhas. No entanto, no médio e longo prazos, os benefícios serão visíveis e importantes para a fluência da cadeia produtiva.
Por que ela é tão importante?
A análise de falhas é determinante para o sucesso da gestão de manutenção na indústria. Ela garante a produtividade das máquinas, a qualidade dos produtos e, consequentemente, a satisfação dos clientes. Como todo processo empresarial, a estratégia de dar atenção especial aos defeitos antigos — a fim de evitá-los no futuro — impacta positivamente outros setores, como o financeiro e o de vendas. Veja algumas vantagens!
Diminui a recorrência de falhas
O primeiro benefício da utilização dessa estratégia é a diminuição de problemas. Como complicações que por ventura ocorrerem serão monitoradas e estudadas, a manutenção preventiva vai aumentar para evitar que falhas semelhantes ocorram novamente.
Aumenta a produção
É fato que defeitos ou falhas podem acarretar a interrupção de equipamentos, o que deixa a produção comprometida. Por isso, investir na análise desses problemas fará com que a produção seja mais fluente e só seja interrompida devido a poucas exceções.
Redução de custos
Outra consequência positiva da realização de algum método de análise de falhas é a redução de custos. Quando uma irregularidade é detectada no começo, as chances de correção imediata são bem maiores. Sem contar que a adoção de ações preventivas evita maiores prejuízos e reduz custos de manutenção.
As 7 fases da análise de falhas
A análise de falhas, independentemente do método usado, segue algumas etapas sistêmicas para que o processo seja feito de forma coerente e eficaz. Cada método tem suas particularidades, mas todos eles têm o mesmo objetivo final. Cabe à equipe de manutenção decidir qual deles usar, porém, sempre observando as fases a seguir.
1. Especificação do problema
A primeira parte de uma análise de falhas é especificá-la e detalhá-la, por meio de uma documentação que inclui a descrição do problema com todas as suas características — quanto mais detalhes tiver, melhor. É interessante que tudo que puder constar do histórico do equipamento esteja na especificação.
2. Elaboração de hipóteses
Depois de detectado e especificado o defeito, a próxima etapa é elaborar as hipóteses do que causou o problema. É importante elencar todas as possibilidades, inclusive com base em falhas semelhantes que já ocorreram.
3. Verificação de hipóteses
Uma vez descritas e comparadas as hipóteses, é a hora de investigar quais delas são mais prováveis ou não. Essa averiguação deve levar em conta as condições do equipamento, o modo como ele era operado, sua capacidade operacional, entre outros detalhes.
4. Análise dos controles existentes
Uma boa gestão de manutenção oferece sistemas de controle e fiscalização das máquinas e até dos processos existentes. Diante de uma falha, isso também deverá ser observado e estudado, afinal, o equipamento pode ter apresentado alguma anomalia identificável nessas inspeções.
5. Avaliação de índices das falhas
Os índices de falhas vão aparecer no histórico de cada máquina. Ali, devem estar especificados os defeitos e problemas ocorridos anteriormente, quantas vezes aconteceram ao longo de determinado período e quais foram as soluções encontradas.
6. Elaboração das ações de correção e prevenção
Se for uma deficiência nova, ações de correção devem ser elaboradas. Em casos de reincidência de problemas, a questão está nas práticas preventivas que precisam ser pensadas para que o defeito pare de aparecer com frequência.
7. Acompanhamento das ações adotadas
Por último, após a implementação das intervenções pretendidas, é imprescindível monitorá-las. Pode ser que elas não surtam o efeito desejado ou precisem de algum tipo de ajuste ou readequação. Esses processos são fáceis de aplicar e garantem um efeito muito positivo no final de cada ciclo. No entanto, precisam ser feitos com engajamento e consistência pela equipe envolvida.
Como fazer na prática?
Na rotina industrial, os métodos mais usados para fazer a análise das falhas são os seguintes:
- Análise de Modos de Falhas e Efeitos (FMEA): tem como objetivos identificar as falhas de um produto ou processo, suas causas e seus efeitos, para preveni-las e analisar os riscos de ocorrência;
- Cinco Porquês: determina a causa e o efeito de uma falha em particular. Geralmente, é encontrada ao final da resposta de cinco perguntas. É válido para peças e componentes, mas ineficaz para causas humanas;
- Espinha de Peixe: técnica que utiliza um gráfico que determina 6 possíveis causas — máquina, mão de obra, medidas e dados, condições de operação, método e material e seus efeitos mais prováveis.
Existem outros métodos igualmente úteis e aplicáveis. No entanto, os gestores de manutenção devem optar pelo mais apropriado e eficaz para solucionar cada problema.
Suponhamos que uma máquina empacotadora apresente um defeito na hora de finalizar o fechamento da embalagem, e a equipe de manutenção decide usar a técnica FMEA.
A máquina não fecha a embalagem, essa é a falha. O produto chega aberto para o cliente, que vai reclamar e devolvê-lo, esse é o efeito. Na devolução, a falha é detectada. É nesse momento que o processo vai entrar nas 7 fases que mostramos.
A análise de falhas é primordial para o sucesso da gestão de manutenção e para a elaboração de práticas preventivas e corretivas. Além disso, estabelece um histórico comparativo e indicativo de procedimentos que devem ser adotados em situações similares. Os benefícios dessa estratégia são amplamente verificados no médio e longo prazos.
Gostou de aprender sobre análise de falhas? Quer saber mais sobre manutenção e outros assuntos? Assine a nossa newsletter e receba, em primeira mão, nossos conteúdos exclusivos!